PPGI (Pre-Painted Galvanized Iron) coated coil is a type of steel coil that has been coated with a layer of zinc to prevent rusting and then painted with various colors and finishes. The process involves several steps:
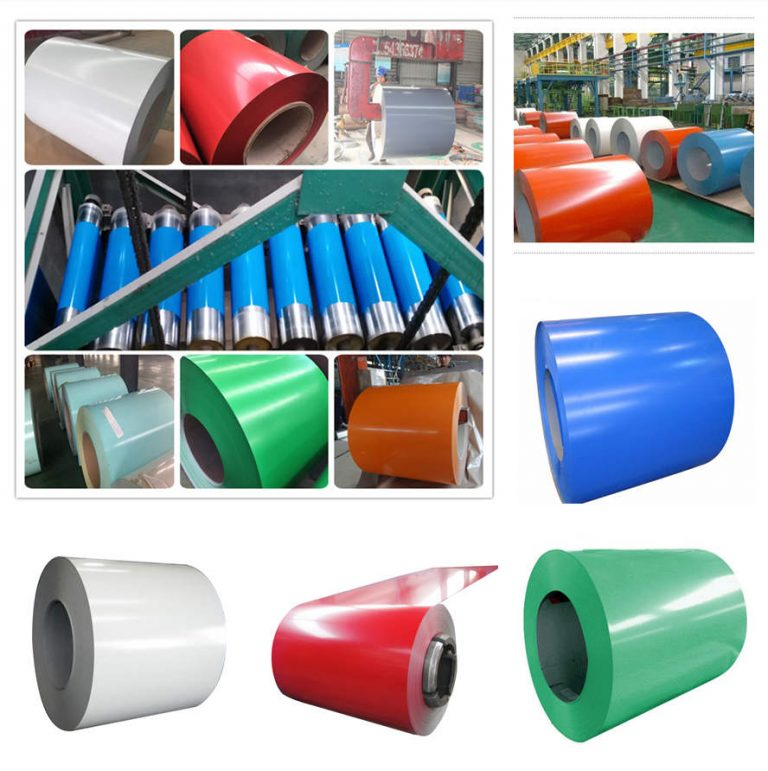
Manufacturing Process
- Base Metal Preparation:
- Cold-Rolled Steel (CR Steel): The base metal used is typically cold-rolled steel, which provides good mechanical properties and surface finish.
- Hot-Dip Galvanization: The steel coil is passed through a molten zinc bath, creating a zinc coating that adheres to the steel surface, providing corrosion protection.
- Chemical Treatment:
- Surface Cleaning: The galvanized coil is cleaned to remove any contaminants such as oil, dirt, and residues.
- Chemical Conversion Coating: A chemical treatment (usually chromate or a non-chromate alternative) is applied to the cleaned surface to enhance the adhesion of subsequent layers and further improve corrosion resistance.
- Primer Coating:
- Application of Primer: A layer of primer is applied to the chemically treated surface. This primer is usually an epoxy or polyester type that offers good adhesion and corrosion resistance.
- Curing: The primer-coated coil is then passed through an oven to cure the primer, ensuring it is properly adhered and hardened.
- Topcoat Painting:
- Application of Topcoat: The final paint layer, known as the topcoat, is applied. This layer provides the desired color and finish (glossy, matte, textured, etc.).
- Curing: The topcoat is cured in an oven to ensure it adheres well and achieves the desired durability and appearance.
Characteristics and Benefits
- Corrosion Resistance: The zinc coating provides excellent protection against rust, while the primer and topcoat add further protection.
- Aesthetic Appeal: PPGI coils come in a wide range of colors and finishes, allowing for aesthetic versatility in various applications.
- Durability: The multi-layered coating system ensures long-lasting performance, even in harsh environments.
- Formability: PPGI coils can be easily formed and fabricated into various shapes and profiles, making them suitable for a wide range of applications.
Applications
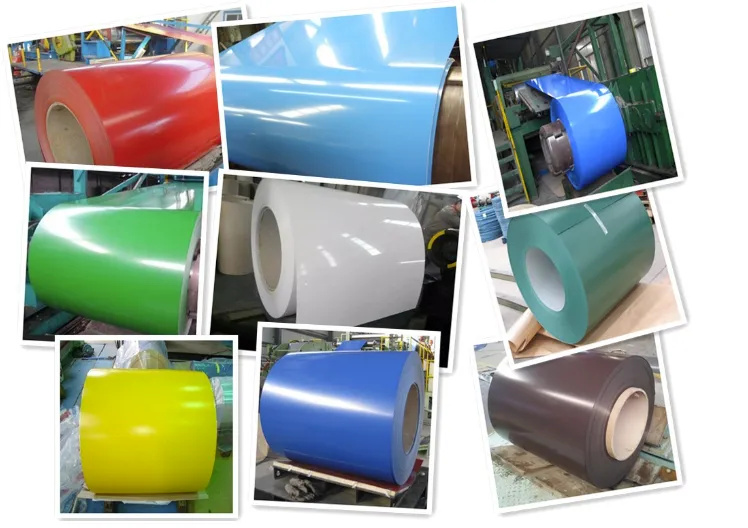
- Construction Industry:
- Roofing and Wall Cladding: PPGI coils are commonly used for roofing sheets and wall cladding due to their durability and color options.
- Building Facades: They provide an attractive and durable solution for building exteriors.
- Home Appliances:
- Refrigerators, Washing Machines, Air Conditioners: The aesthetic appeal and corrosion resistance of PPGI coils make them ideal for household appliances.
- Automotive Industry:
- Car Body Parts: PPGI coils are used for manufacturing various automotive parts due to their formability and corrosion resistance.
- Furniture:
- Office Furniture, Shelving: The durability and wide range of colors make PPGI coils a good choice for furniture manufacturing.
- Other Applications:
- Electrical Cabinets, Signage, and More: PPGI coils are also used in the production of electrical cabinets, signage, and other industrial applications.
Quality Standards and Specifications
PPGI coils are manufactured to meet various international standards, ensuring consistent quality and performance. Some of the commonly followed standards include:
- ASTM: American Society for Testing and Materials
- JIS: Japanese Industrial Standards
- EN: European Norms
Maintenance and Handling
- Handling: Care must be taken during handling and storage to avoid surface damage. PPGI coils should be stored in a dry and clean environment.
- Maintenance: Minimal maintenance is required. Regular cleaning with mild detergents can help maintain the appearance and longevity of the coated surface.
The PPGI coils offer benefits such as easy installation, low maintenance, and long-lasting performance, making them a popular choice in the construction and manufacturing industries.